7 features to look for in a software for Ex inspections
In the oil and gas industry, selecting the right software for your Ex inspections is important for ensuring safety, compliance, and operational efficiency.
Here are 7 key considerations to prioritize, when you are looking for a maintenance and asset management software in hazardous areas.
1 - Compliance assurance
Ensure the software includes built-in compliance tools specifically tailored to Ex inspection requirements in the oil and gas industry, helping to maintain regulatory compliance and ensure workplace safety.
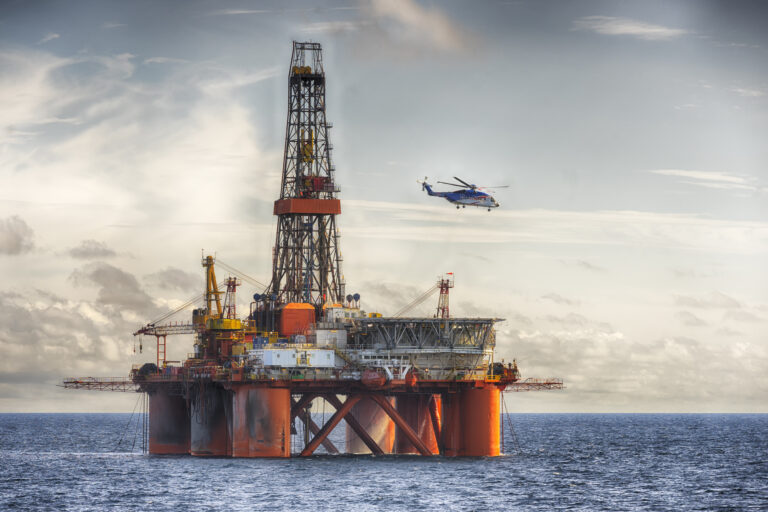
2 - Tailored asset management
Ensure the software offers robust asset tracking and management capabilities tailored to the oil and gas industry, including equipment hierarchy, maintenance history, and asset performance analysis.
Make sure that your software provides standard checklists and seamlessly allows the integration of bespoke checklists:
- Hazardous Electrical IEC 60079-17
- Hazardous Non Electrical ISO 80079-36
- Electrical Installations IEC 60364
- Your bespoke checklists
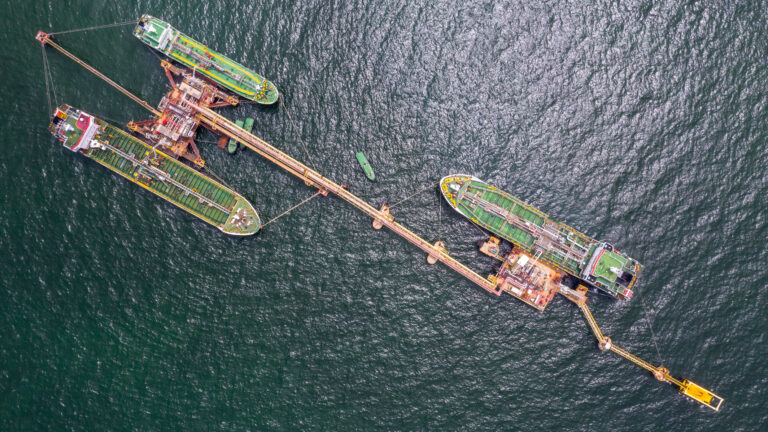
3 - Scheduled & maintenance planning
Look for features that enable efficient scheduling and execution of preventive maintenance tasks, helping to minimize downtime and extend asset lifespan.
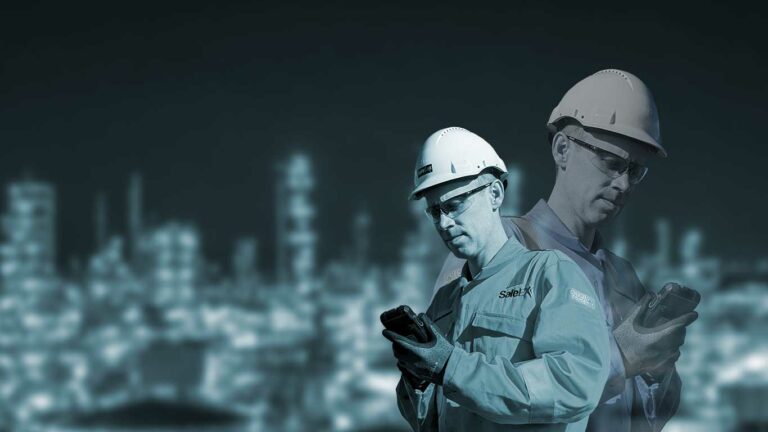
4 - Work order management
Choose software with streamlined work order management functionalities, allowing for easy creation, assignment, and tracking of maintenance tasks, including Ex inspections.
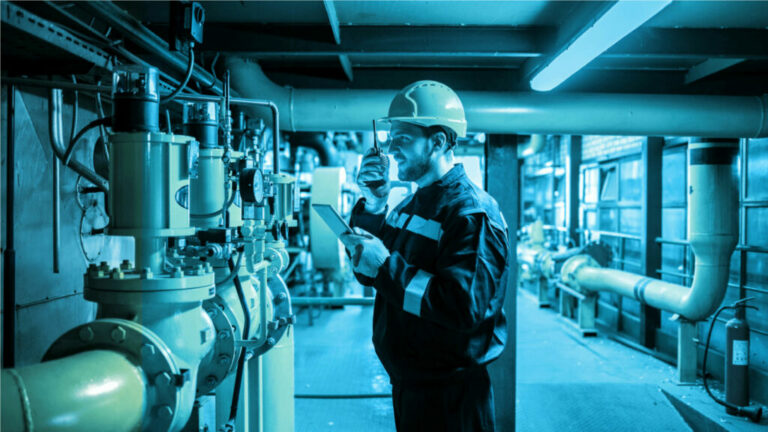
5 - Mobile accessibility
Prioritize a solution that provides mobile access, empowering field personnel to conduct inspections, submit work orders, and access critical data from anywhere, enhancing productivity and efficiency.
Choose a software that allows technicians to work with their Ex mobile devices offline offshore with no WiFi needed.
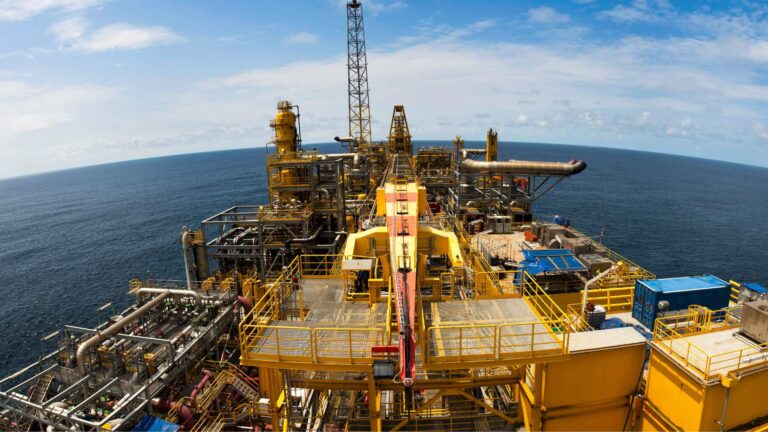
6 - Easy integration
Choose a solution that via REST API can seamlessly integrate with existing systems and workflows, such as asset management, ERP, and SAP platforms eliminating having to work in multiple systems.
Integration ensures data consistency, eliminates silos, reducing resource hours, and enhances collaboration across departments, leading to more efficient operations.
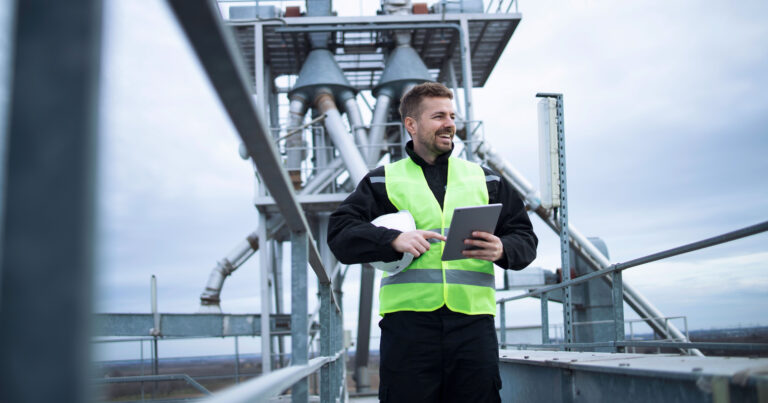
7 - Reporting and analytics
Select a solution with instant reporting and analytics capabilities, enabling you to gain actionable insights from maintenance and inspection data, identify trends, and make informed decisions to optimize asset performance and safety.
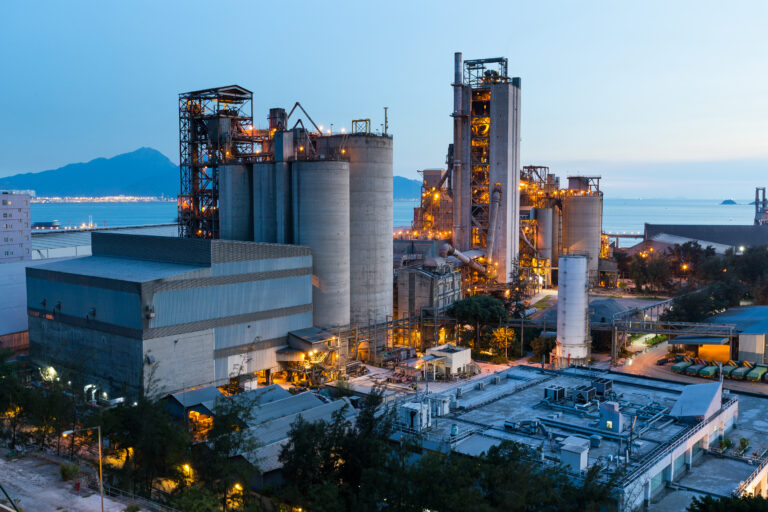
Simplify your Ex inspections
SafeEx Cloud offers a solution to meet the specific needs of maintenance and Ex inspection in the oil and gas industry in the oil and gas industry. SafeEx Cloud ensures a safe, compliant and cost reduced operation. Book a demo
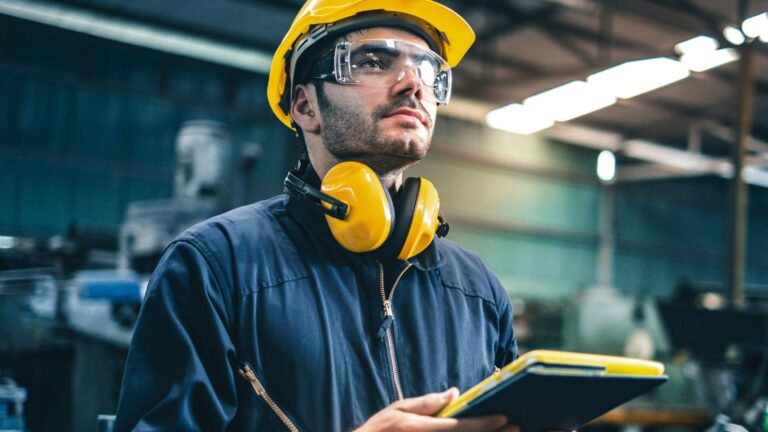